Project Info
COMPLETE
Project Title
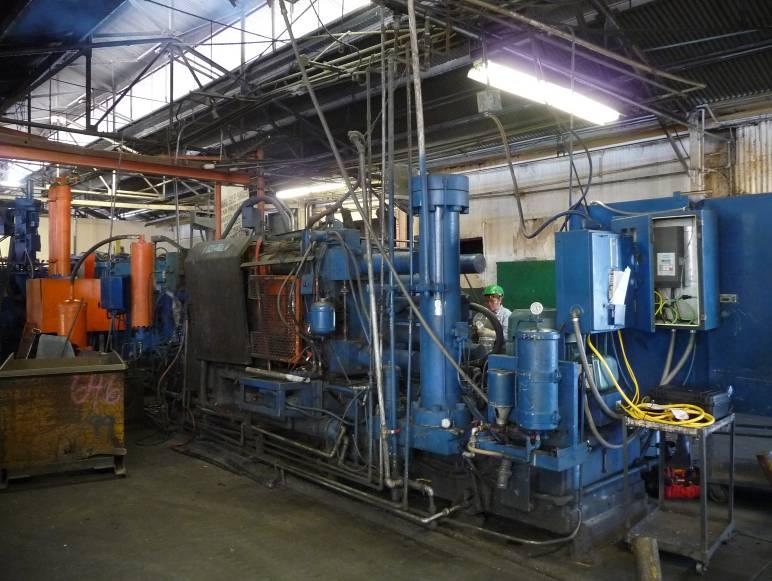
VSD for Die Casters
Project Number ET10SCE1070 Organization SCE End-use Process Loads Sector Industrial Project Year(s) 2010 - 2010Description
Conventional die casting machines do not have variable speed drives on motors for changing pressures for hydraulic pumps. The VSD can control the speed of motors to open, close, and clamp the molds during casting. When the mold is clamped, a mechanical system (such as latch) provides the holding pressure; therefore, the motor does not need to run at full speed at this mode. The clamping mode is typically accounts for more than 50% of a casting cycle; thus, it allows us to save energy by installing a VSD. This project, therefore, evaluates the effectiveness of VSD on die casting machine.
Project Results
A die-casting machine (DCM) is typically driven by a complex hydraulic system to produce dimensional metal parts accurately. The design of a DCM is mainly driven by high-volume production and shot capacity1 ; the low production cost of each casting allows the DCM owner to make a profit. Until the early 90's, high-volume orders enabled DCM owners to invest in advanced die casting machines. Unfortunately, the global economy has changed the nature of the die casting business in the United States, particularly in California, and now other countries produce high-volume orders; therefore, the survival of die casting companies in California heavily relies on frequent customized designs and small-volume orders. Die-casting companies are looking for methods to reduce the production cost per casting by making various improvements such as increasing energy efficiency.
The goal of this project is to improve the energy efficiency of existing aging DCMs by retrofitting a variable speed drive (VSD) on the DCM's hydraulic pump motor. This project evaluates the VSD measures' ability to provide energy savings when the speed of the hydraulic pump motor varies, or is controlled based on the DCM's hydraulic pressure and flow rate requirements.
Southern California Edison (SCE) conducted a field evaluation where the energy efficiency of an existing aging DCM was measured. A baseline was established by examining the typical operation of an existing DCM's performance after being retrofitted with a VSD while still maintaining the typical operation.
The selected DCM is a modified Harvill2 Model 406 that is over 20 years old. Its locking pressure capacity is 400 tons (US) and the maximum shot capacity is 14.3 pounds (lbs) of (aluminum). The hydraulic pump is driven by a 6-pole, 40 horsepower (hp), 480 Volt (V), and 3-phase motor. In order to establish a fair comparison, we replaced the existing motor with a National Electrical Manufacturers Association (NEMA) Premium® motor with the same specifications. Thus, the baseline is the conventional operation mode of an existing DCM when retrofitted with a new hydraulic pump motor.
Because the DCM does not produce the same casting for more than 1 or 2 days, low-volume die casting orders created a measurement challenge during this evaluation period. Therefore, one-day measurements were designed in order to capture a fair comparison between a DCM with the VSD installed and one without. The energy consumption of the DCM without the VSD installed while producing the same number of castings as the DCM with the VSD was monitored.
Project Report Document
Loading PDF Preview...