Project Info
COMPLETE
Project Title
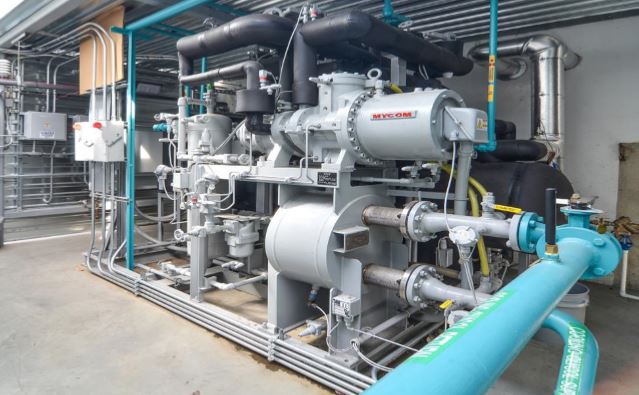
Ammonia/CO2 Refrigeration System Evaluation at a Food Processing Facility
Project Number ET13SCE1230 Organization SCE End-use HVAC Sector Commercial Project Year(s) 2013 - 2016Description
Evaluate performance of HVAC and refrigeration applications using advanced refrigerants. This project intends to explore and document advances in product development for advanced refrigerants in the refrigeration and HVAC applications.
Project Results
The HVAC&R world is undergoing significant changes, with regulatory bodies moving to reduce the use of refrigerants with high global warming potential (GWP). In commercial and industrial applications, ammonia refrigerant is a common solution which has zero GWP, but its applicability is limited because of mild flammability and toxicity concerns. In these applications R404A and R507A are common refrigerants today, but because of their high GWPs they face growing regulatory restrictions.
This report describes a field test of an alternative technology: a system using ammonia as the primary fluid and CO2 as a pumped volatile secondary fluid. This allows the ammonia charge to be much smaller than an equivalent all-ammonia system, while distributing only CO2 into the building. The system was installed in a food production facility in Irvine, California and is monitored along with existing, baseline conventional-refrigerant equipment, to study performance. The study documents the findings of differences in energy and power consumption as well as observations and learnings from the process of transitioning from a baseline system to a new, alternative-refrigerant approach.
The new refrigeration system was installed to provide cooling for an existing a 2,100 squarefoot, -20°F drive-in freezer. The existing refrigeration equipment, part of a R507A system, was left in place but shut off. Instrumentation equipment was installed to monitor the performance of both the new system and the existing equipment, and the new equipment was disabled periodically during the study to allow collection of baseline data.
The new system used less energy in similar operating conditions than the baseline equipment, as shown in the stacked-bar chart in Figure 2. This figure shows the total daily energy consumption of each sub-component. Comparing days in April with similar weather, the baseline system used 220 kWh more per day than the new equipment, a savings of 21%. During hotter weather in summer, the savings was 16-25%.
The project also included simulated demand response events, including pre-cooling and load shedding. This was performed manually on-site with the help of the host facility personnel. The temperature set-points in the freezer were adjusted by about 5°F in either direction. The control was simple set-point adjustment. An example of a result comparing a pre-cool and shed event with typical baseline days is shown in Figure 3. Several different durations were evaluated. The average power during the events was 14-21 kW lower during the first hour than the same baseline hours.
The ability to pre-cool was limited by the pressure setting of the CO2 receiver, which could not be quickly adjusted for these evaluations. Since the CO2 liquid is held at a fixed pressure, the supply temperature in the freezer is limited by that pressure; subsequent research efforts should evaluate the effect of adjusting this pressure setting to further pre-cool.
The ammonia and carbon dioxide system evaluated here provided significant energy savings while using two refrigerants that are environmentally friendly and not subject to increasing regulatory and environmental pressures. The system remains in place and the host has, since project completion, added an additional freezer space which is only cooled using the new ammonia/carbon dioxide system, with no R507A backup.
Project Report Document
Loading PDF Preview...