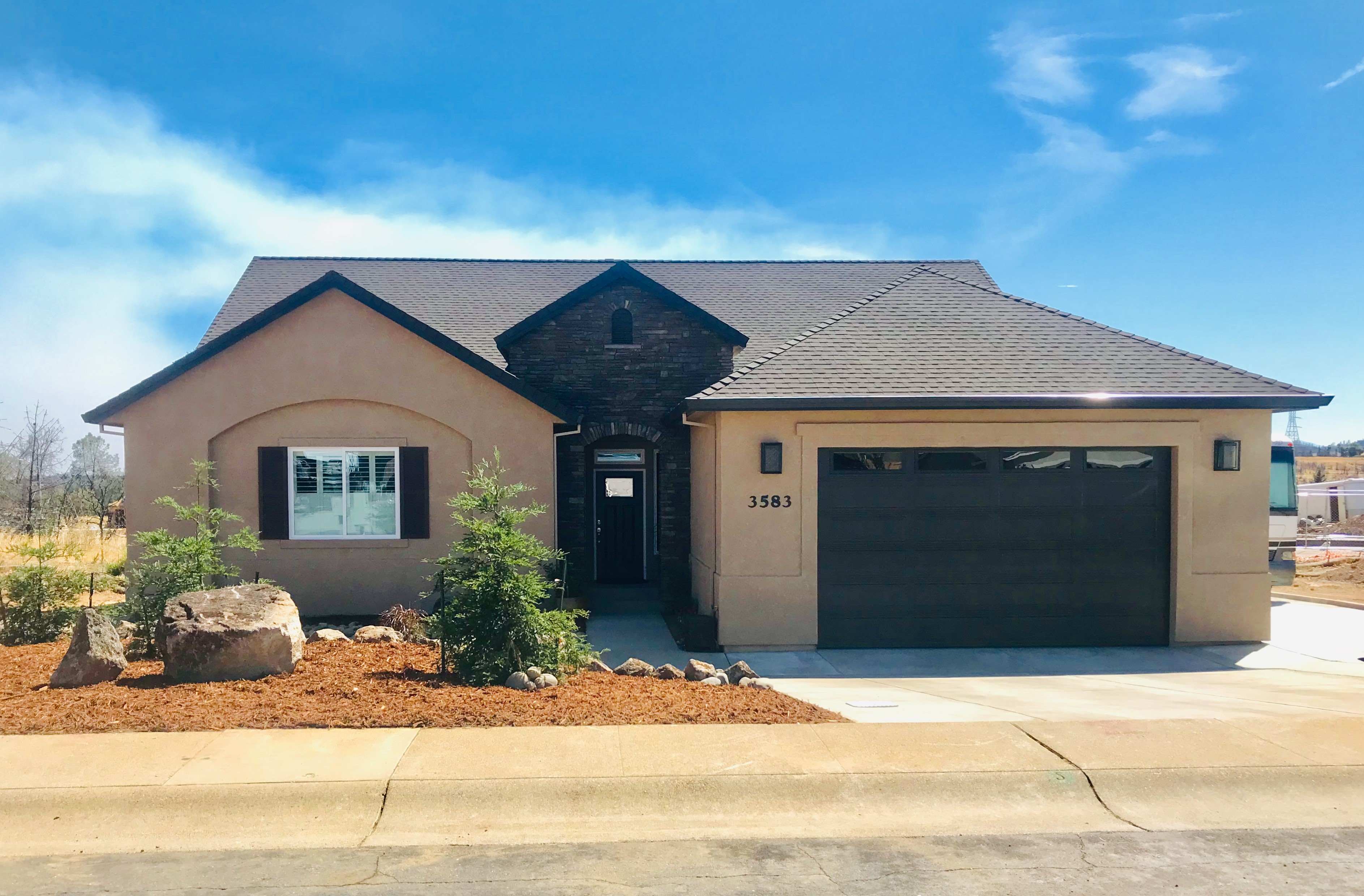
All-Electric High-Performance Home: Redding, California Site Monitoring Report
Project Number CR19PGE1071 Organization PG&E End-use HVAC, Lighting, Water Heating/DHW/HPWH, Whole Building Sector Residential Project Year(s) 2019 - 2021PG&E’s Code Readiness subprogram strives to collect data on measures and technologies that will support more robust advocacy in future code cycles rulemakings as well as inform voluntary energy efficiency programs. Additionally, by encouraging residential builders and commercial building owners or developers to enlist in this effort, participants gain first-hand experience with installation, code compliance, and performance characteristics of these advanced measures.
The primary objectives of this Code Readiness residential project were to:
- Assess the performance of an ultra-efficient all-electric building design implemented by a leading high performance home contractor,
- Assess builder response to the installed measures (costs, installation issues),
- Document commissioning data,
- Report on full year occupied home monitored energy use by end use, and
- Compare annual energy end uses to compliance model projections.
To achieve this, the energy use and comfort performance of a high-performance home built by a leading high performance home contractor (Mike MacFarland of Energy Docs) in Redding, CA was monitored. The installed measures in the 2,372 ft2 single-story home, located in Redding, CA, included:
- High performance exterior walls: 2x6 framing, 24" on center with blown in blanket fiberglass cavity insulation and R-4 rigid exterior insulation (resulting in an ~R-25 wall)
- Thermal envelope air sealing: Attention to detail with continuous plywood wall sheathing, taped & sealed air barrier, caulked and foamed. Leakage target of 1.0 ACH50.
- Attic insulation: R-60 ceiling insulation with radiant barrier; energy heel truss design
- Raised floor construction: R-19 insulated foundation wall (3 inches of polyisocyanurate)
- Efficient windows: 10% glazing area with U values ranging from 0.23-0.25, and SHGC from 0.20-0.30.
- Mechanical space: Dedicated equipment space within the indirectly conditioned crawlspace contained HVAC equipment and all ducts.
- Right-Sized Ducted MSHP: one ton slim duct mini-split located in crawlspace (equipment sizing at 2,366 ft2/ton)
- Heat Recovery Ventilation: Heat recovery ventilator located within laundry room closet (heat recovery minimizes ventilation thermal loads on conditioned space and improves air quality due to filtration).
- Heat Pump Water Heating: 1.25 ton CO2 heat pump water heater (HPWH) with a 3.84 Energy Factor rating; unit is a split system with thermal engine located outside and 83 gallon storage tank centrally located in laundry room to minimize distribution losses.
- All-electric Appliances: All-electric efficient appliances including an induction cooktop and heat pump clothes dryer
- Lighting: All integrated LED lighting
This project builds off a prior PG&E project completed in 2018 on a similar sized custom home in Redding where an ultra-high-performance wall system was implemented. The current project intentionally backed off on some of the more aggressive measures implemented in the 2018 project. During construction of the 2018 house, Mr. MacFarland provided direct on-site oversight of installers. With this house, installers were required to follow detailed framing and HVAC designs, but without direct oversight, as would be more typical in residential construction. In addition to the monitoring results, Mr. MacFarland provided his own evaluations and observations of the ability of local tradespeople to implement more advanced energy efficient designs, as well as feedback from the homeowners on performance and comfort.
Monitoring Results
Monitored electrical consumption over the year (August 2019–July 2020) totaled 14,980 kWh with PV generation during that period totaling 12,392 kWh (83% of the way to Zero Net Energy (ZNE). Energy usage included 5,426 kWh for “plug” loads (of which 3,486 kWh was used by the pool pump and hot tub). However, excluding these two lifestyle choice amenities, the house would have easily achieved ZNE. Space conditioning energy use amounted to only 2,612 kWh for the year, which is impressive for the extreme summer climate in Redding (Climate Zone 11).
Despite the low summer cooling setpoints selected by the occupants (typically 70°F), indoor conditions were maintained within ±3 °F of setpoint for the full duration of the monitoring period. This result is impressive given the HVAC system size and highlights the quality of the HVAC design and implementation.
Key Project Takeaways
The resulting performance of the all-electric ZNE design presents a robust case for what can be accomplished with local tradespeople in high performance residential construction with a focus on climate-specific and detailed design. Whereas the previous 2018 Redding house represented a cutting-edge integrated design approach, demonstrating what can be achieved by some of the best contractors and installers in the industry, this project demonstrated how best practices can be implemented in the production home environment.
Production home performance would benefit from this strategy of precise design documentation. In the moment of replicating plans simultaneously at several sites across a development, tradespeople cannot be expected to “fill in the gaps” by researching and implementing best practices themselves. Instead, tradespeople simply implement plans as presented to them in plan documentation. Therefore, as demonstrated by this project, if plans are detailed and specify best practices, the tradesperson will implement that greater detail using best practices, resulting in superior high-performance work.